Process
Why Our Process Works
Every new project, whether bulk basics or custom builds, goes through our 6-stage APQP process developed based on the needs of customers throughout planning and production. Our stages ensure we exceed expectations with both internal and customer checkpoints and reviews along the way.
Stage 1: Project Definition
Stage 2: Product Design & Development
Stage 3: Process Development
Stage 4: Product and Process Validation
Stage 5: Production
Stage 6: Continuous Improvement
Project Definition
RFQ, Drawings/Specifications Review, Feasibility, Analysis, Quote / PO.
Product & Process Design
Project Timing, BOM, Design Review, Resource and Equipment Needs, Supplier ID, Install, Tooling Launch.
Validation & PPAP
Trial Runs, Supplier PPAP/Material In-House, Resources Trained, PPAP to Customer.
Production
Pre-production Shipments, Start of Production, GP12, Series Production.
Our Driving Forces
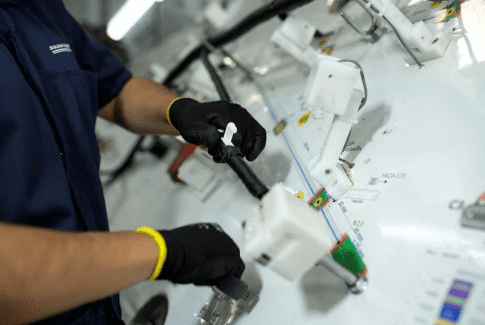
Quality
Quality Management and performance is a critical element to Julian Electric gaining and retaining business relationships. The core tenets of this system include:
- Culture of quality throughout organization
- Incoming, In-process and Final Inspection Processes
- Error proofing methodologies
- Weekly and Monthly KPI review and communication
- Training process to develop competencies for Julian workforce: Knowledge,
- Skill, Experience & Attitude
- Corrective/Preventive Action Processes
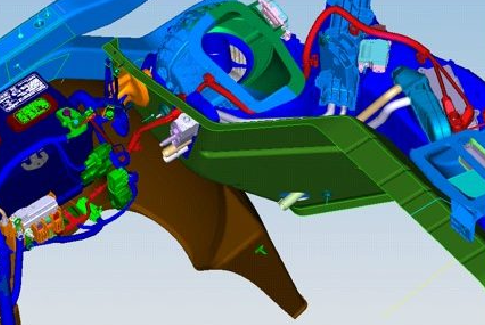
Engineering
Process and Product Engineers at Julian Electric are key drivers of the pre-production process as well as improvement projects throughout the company.
- JEI follows the full APQP process for new parts and projects
- Work closely with customers to support design, prototype and pilot phases
- Reverse engineering of existing products and designs
- Customized layout and testing boards and fixtures
- Customized tooling for a variety of applications
- Trained in the AIAG core tools
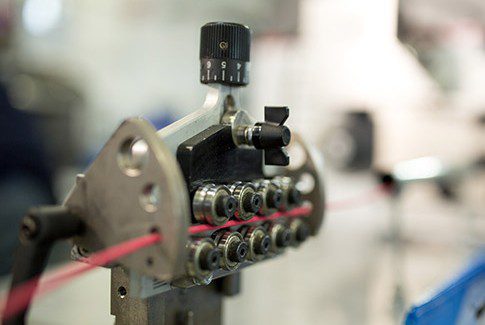
Production
A strong production system is critical in order to support Julian Electric’s customer base and the rapidly changing requirements in various industries. The following principles allow JEI to remain adaptable to these requirements:
- Lean manufacturing philosophies
- Streamlined and balanced production
- Build to job, not stock: allows for rapid turnaround on orders and quick revision change implementation
- Regular Kaizen events at all levels of organization
- Internal Six Sigma training
- Safety Committees
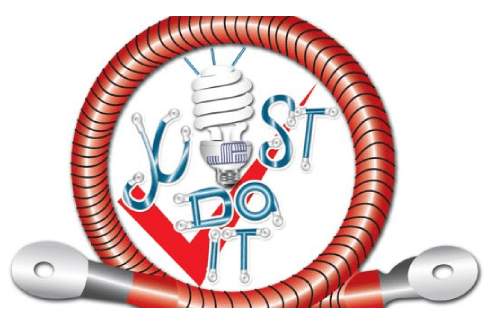
Continuous Improvement
Julian Electric understands the need for continuous improvement across all company processes. This effort is integral to the daily operations at all Julian Electric facilities and includes the following:
- Comprehensive Continuous Improvement program
- Regular Kaizen and 5S initiatives throughout the organization
- Julian Electric’s internal “Just Do It” program encourages suggestions for improvement from all levels of the organization
- Best improvement ideas earn incentives